My Motivation
Robotics and electronics are part of my everyday life. Whether its a side project I’m working on, the work I’m doing for my job, or the school work I’ve done, it is something that has seemingly always been important for me. I have tried to detail all of the main projects I have worked on for others to be able to copy/emulate, and I hope this provides someone with the drive to try something new!
Five Bar Robotics for Air Hockey
My honors thesis was to build a five bar robot to play air hockey. To do this, I first had to develop a base of mathematical tools to understand the performance of such a device. From there, I designed custom BLDC motors to achieve that task. Once I had designed the motors, I could design the robot and size the components to the motor specification and the simulation tools I had developed. At the end of all of this, I was finally able to machine and build everything (including the air hockey table) and get it working after about 2 weeks of programming!
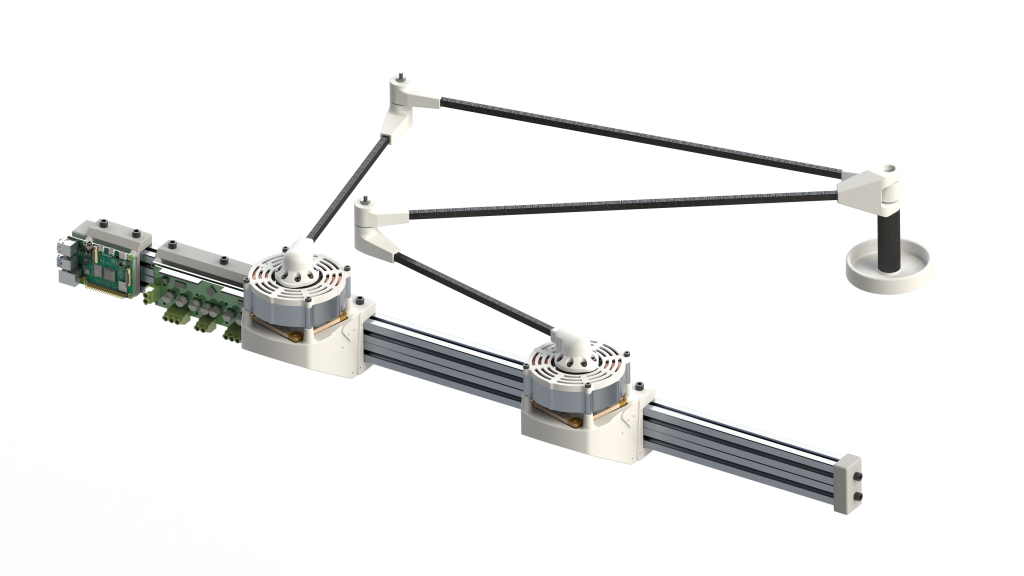
The final robot used vision from a Flir camera above the air hockey table to identify the puck and play defense. This was implemented on a Raspberry PI running Ubuntu Mate and ROS2, along with a code repository I helped develop. Once I get some high quality pictures and video of it performing, I’ll include those here. I did all of the design work on the robot, and had two of my friends help with the programming and machining of the robot. A big thanks goes out to them for helping me throughout the build!
Frank the Differential Drive Robot
Because I had the opportunity to work with a professional that has experience in optimal robot pathing, I thought I’d take the opportunity and and do something neat. Meet Frank, the differential drive robot:

Frank is finished from a mechanical, electrical, and programming standpoint (check out this post for more details). His programming is basic and only supports remote control, face tracking, and motion controls. In the future, I’d like to experiment with path planning algorithms and see how accurate I can get, especially if I can use something like SLAM or some other localization methods. The goal would be to create a pathing algorithm to apply to Frank for time optimization. I will likely be using an alteration of the A* algorithm and Bezier spline interpolation. When I eventually get to this, I’ll make sure to make a post about it.
Electric Longboard
Getting around can be hard sometimes, especially when your bike is sort of falling apart and many years too old. Saw one of my friends with an electric longboard and decided I wanted one. After a lengthy design process and relatively quick build, it’s finished! Here is the picture of the finished board!
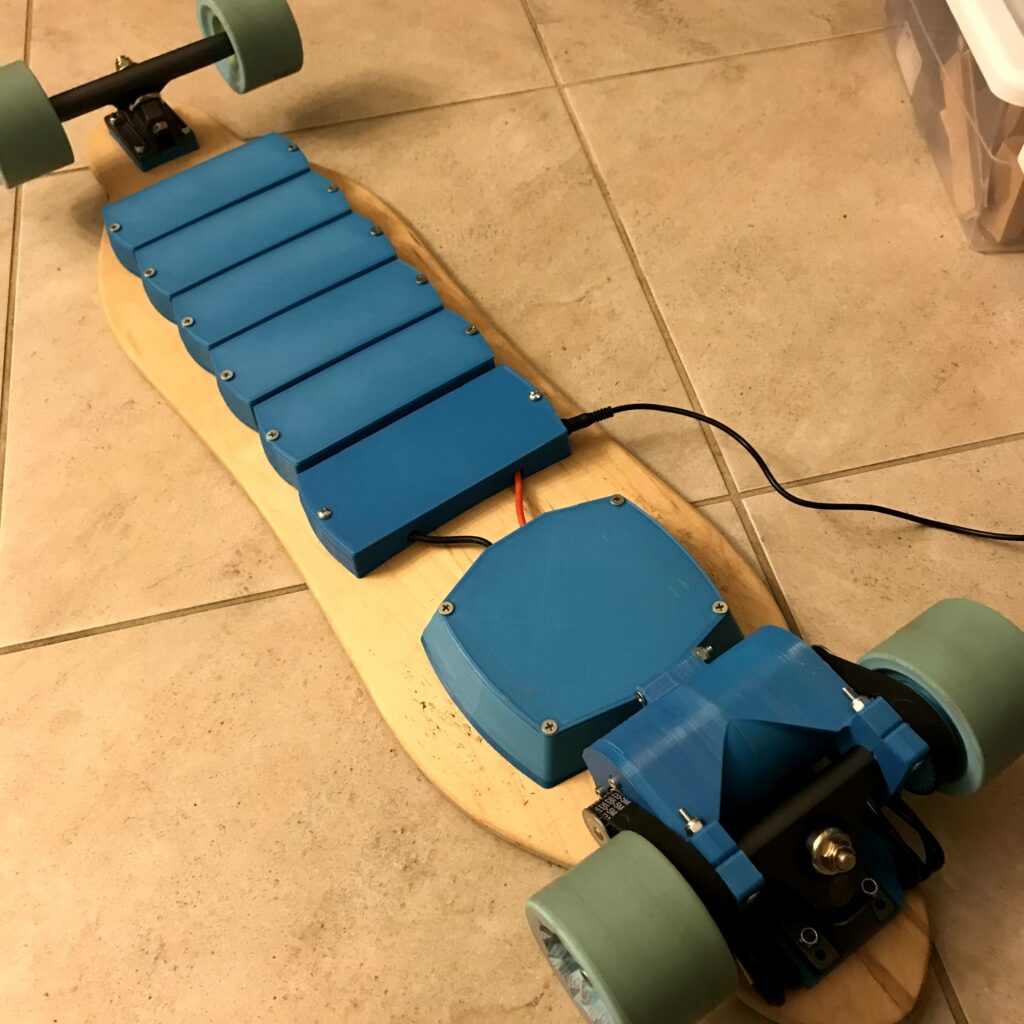
Battery Welder
Have you ever wondered how you’d power your various mobile devices? If you have, you’ve probably realized it’s Battery Time! While a large majority of people would have just bought something off the shelf (OTS), I decided that I wanted a learning opportunity. I learned how to make my own battery spot welder using an open source project I found online and had a lot of fun testing it. (It is easily capable of vaporizing nickel!)
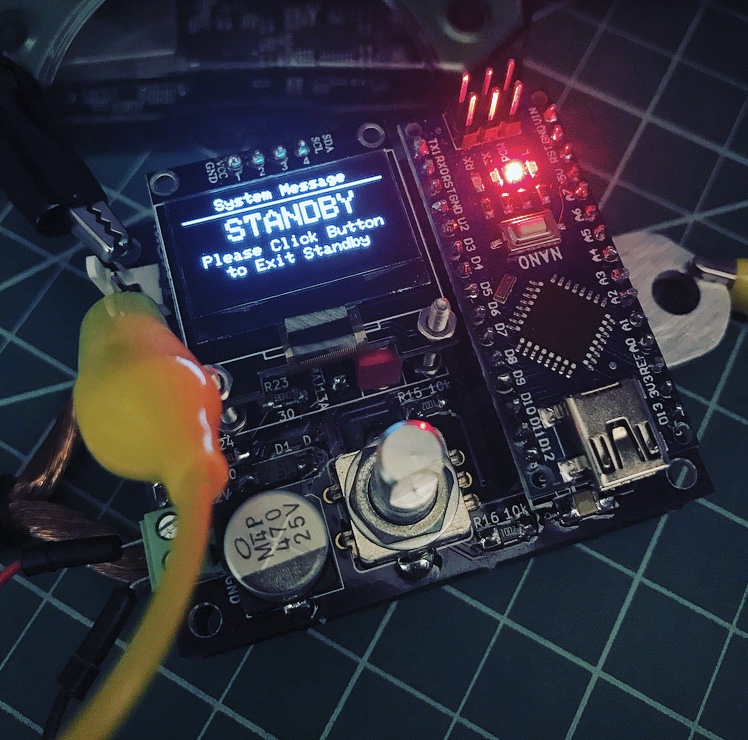
Despite shipping taking nearly an entire semester, I would say the project went pretty smoothly. The only thing I think I may have to do down the line is increase the number of batteries in parallel being used from 2 to 3. It feels a tad “weak” but the welds are strong enough for what I’m doing. I have a few blogs detailing this project and what I’ve used it for here.
FIRST Robotics – FRC Team 1902 Exploding Bacon’s 2019 Robot
My senior year of high school was an incredible experience to say the least. I was the design lead on FRC team 1902 (Exploding Bacon), which gave me an incredible opportunity to oversee the development of our robot. Additionally, in 2019, we also won the Championship level Chairman’s award, placing us in the FRC Hall of Fame. My experience in FIRST robotics set me up to be an engineer and I can’t thank it enough for putting me in such a good position.

We made several changes to the robot over the course of the 8 weeks before worlds, and I’m proud of the final product. At some point I plan on making several posts on the development process of the things I specifically worked on, but for now, here are some quick stats.
- The robot in CAD has 1370 parts including fasteners
- There were 5 revisions of the ball intake
- There were 3-4 revisions of the hatch panel intake
- We cut 25-30 lb of weight in the first two competitions
- The robot made it to playoffs at each competition
- We used several manufacturing methods that were new to us
Leading the build and design of this robot gave me many skills that I would not have otherwise, and I’m very grateful for the opportunity I was given by the team. For more robot stats, visit our 2019 blue alliance page. For more information on FIRST robotics, check them out here.